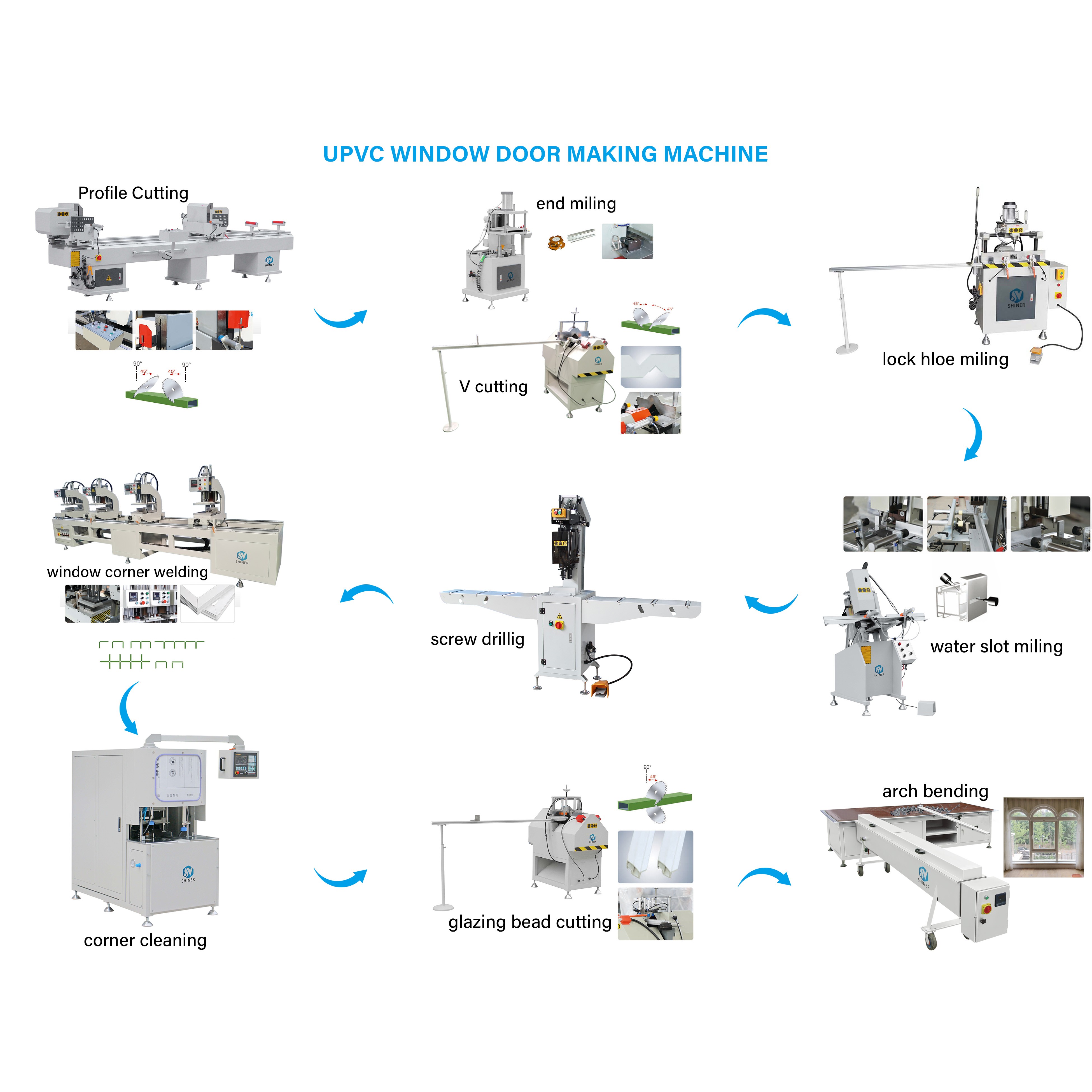
- UPVC doors and windows are manufactured using upvc profiles through processes including cutting machines to cut profile ,installing reinforcement steel ,milling machines to make holes,corner cleaning machines to remove slags,install gasket and hardwares etc.
- Different window types and processing equipment determine varying assembly routes. For example, casement windows and sliding windows have structural differences (profile cross-sections, seals, hardware, installation positions and methods) and require different equipment (casement windows need V-shaped saws for V-cutting middle stiles and cross braces), leading to distinct assembly processes.
- Cutting involves trimming 6m-long profile raw materials purchased from manufacturers to design-specified dimensions using common type cutting machine, heavy duty cutting machine, V-cut, or mullion cutting. Cut profiles should have protected end corners and meet length tolerances (typically 45°±5° for end angles and ±1mm for length) to ensure welding quality.
Milling Drain Holes and Air Pressure Balance Channels :
- Preventing water leakage is a basic function of exterior windows. Milling drain channels and balance channels creates proper drainage paths in frames and sashes to facilitate water/condensation outflow, reducing leakage risks.
- Drain holes are typically milled using Copy Router or Water Slot Machine:To prevent steel lining corrosion, the drainage cavity must remain separate from the main chamber. Drain holes are usually φ5mm×20-30mm oblong holes with staggered inlet/outlet holes, spacing determined by profile systems and window types.
Reinforcing Steel Lining Installation:
- Steel linings play a critical role in enhancing structural rigidity and load-bearing capacity. Installation should follow standards based on profiles, window types, and application environments.
Milling Hardware Holes and Drilling Expansion Bolt Holes:
- Hardware components like locks and Rollers Series are typically installed after steel lining insertion. Hole shapes and positions are determined by hardware specifications. Processing is done using lock hole slot machines. Expansion bolt holes for wall mounting should comply with installation standards. These holes can be drilled using combination screw machines or standard drills.
- Welding joins pre-cut, lined, and milled profiles into rectangular (or special-angle) frames/sashes using hot plate welding machines. As a key process affecting product quality and safety, welding parameters must be optimized for profiles and equipment, with proper sequences to ensure strength and efficiency.
- Corner Cleaning Machines:
- Welding generates excess material (flash) that must be removed to ensure proper sealing and hardware functionality. Deburring should be performed at least 10 minutes after welding to avoid deformation. Finished frames/sashes should be stored vertically at ≥70° angle.
Sealing Strip Installation : Sealing strips (including pile weatherstripping for sliding windows and rubber seals) are critical for thermal/acoustic insulation and airtightness. Installation follows GB/T12002-1989 standards, with most strips installed continuously using manual tools.
Final assembly includes hardware installation, glazing bead preparation, glass/pad installation, and auxiliary component fitting. Special attention is paid to hardware functionality and safety.